AVANT TECNO: Harnessing automation to transition from push to pull processes
In 2022, Avant Tecno decided to automate several processes in their warehouse and production environments to transition from push to pull processes, leveraging the expertise of Rocla AGV Solutions for optimal results. This shift to pull processes in production logistics enhances efficiency by eliminating the need for interim storage, as the IT system now directs items to the right places based on demand and timing.
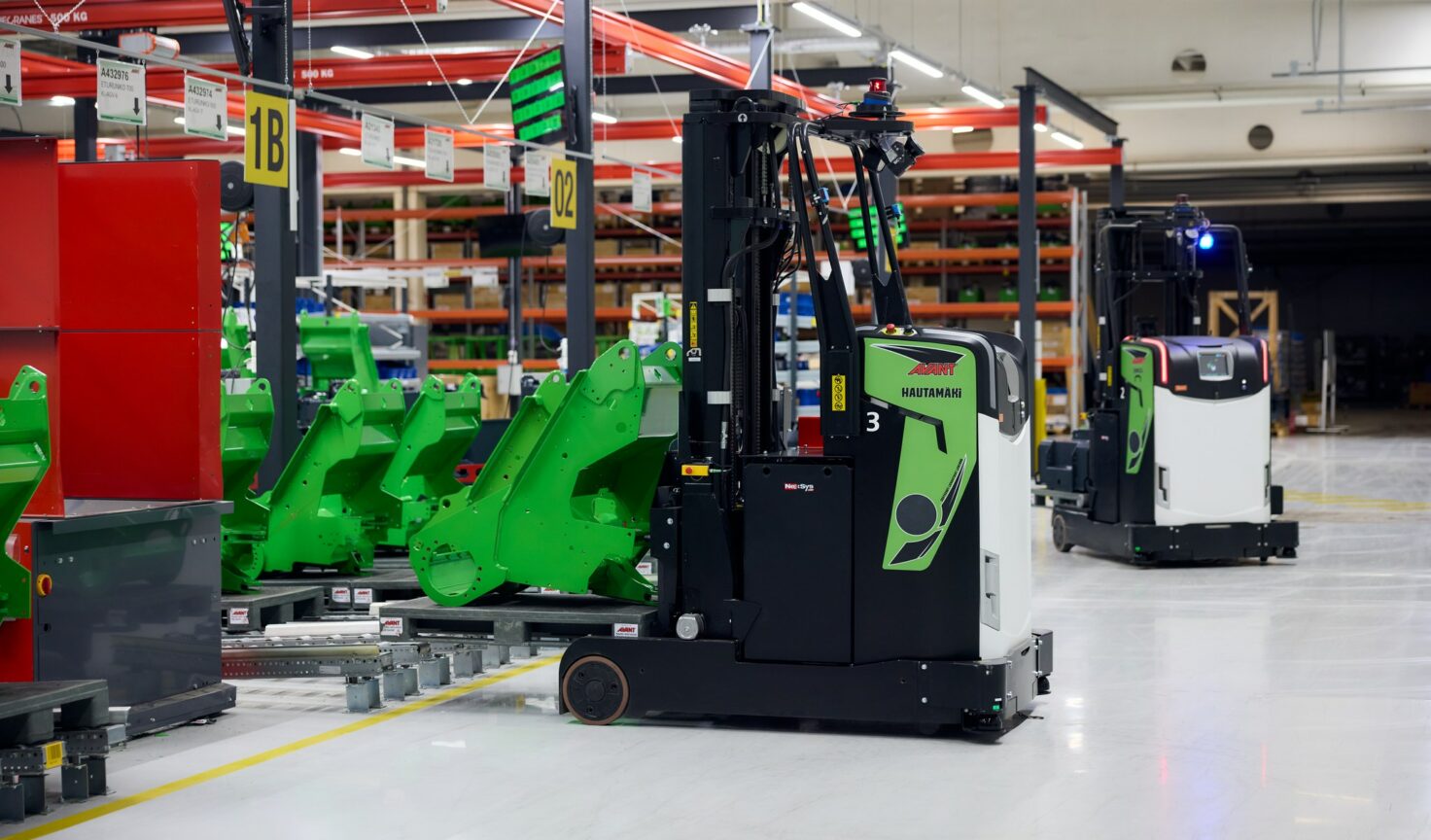
Established in 1991 in Finland, Avant Tecno has grown to become the leading manufacturer of the most multifunctional compact loaders worldwide. With over 80,000 compact loaders produced, the company now offers seven model series, more than 200 different attachments, and over 50 options for the basic machine, all designed to simplify fieldwork.
Due to fluctuating demand and irregular needs, the production line often faced issues with either excess or insufficient inventory. “Our main target was to improve the internal material flow of heavy welded components, such as front and rear frames. These components require several transports and often need to be moved individually due to their size and weight. We aimed to transition into a full pull process where logistics and manufacturing are based on actual consumption at the assembly line,” explains Ari Pesola, Project Manager at Avant Tecno.
To address this challenge and maintain a competitive edge, Rocla AGV Solutions designed a solution consisting of 3 ARTs (Automated Reach Trucks) that would fit into the existing environment, enhancing efficiency and traceability while focusing on optimising inventory management as the primary operational goal.
We realised we could only maximise the benefits of the pull process through the implementation of AGVs
Solution specifications:
- Operative target: optimise inventory management at the production line and increase the overall efficiency of the warehouse and manufacturing environments
- AGVs: 3 Rocla ARTs named by the Avant Tecno staff as Hautamäki, Jönssi, and Dille
- Load: irregular-shaped heavy welded components weighing 250-500 kg
- Aisle width: 3 m
- Racking: standard racking with positions at up to 5.6 m of height
- Operative scope: to automate several flow processes to support production
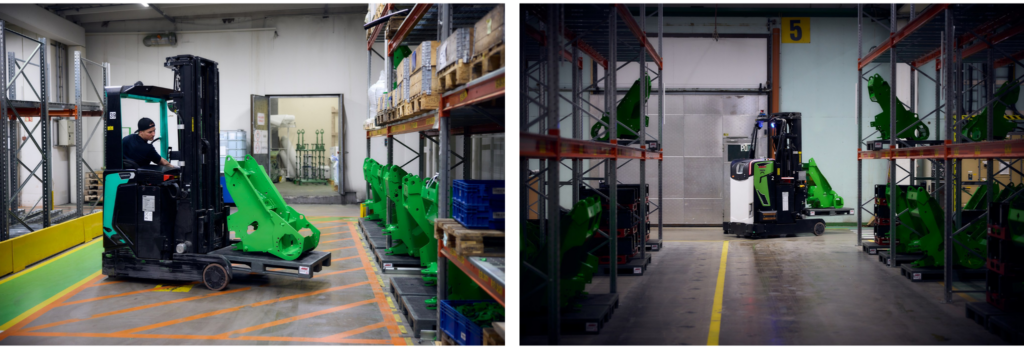
Enhancing existing processes and reaping the benefits
Avant Tecno’s internal logistics rely on several manual forklifts and other vehicles to move smaller components and deliver them to the assembly line. This creates a versatile environment where people and manually operated vehicles coexist and collaborate, often in tight aisles.
Consequently, they wanted an AGVs solution that could operate efficiently in various environments and integrate safely with manual operations. After analysing and studying the existing processes, we designed a solution consisting of 3 ARTs that support and enhance manual operations.
Avant Tecno counts on 3 ARTnf, one of our Rocla Automated Reach Truck models. Our ARTs are ideal for all warehousing operations thanks to having a lifting capacity of up to 10 m, the ability to handle loads up to 1,600 kg and, in some cases, operate in aisles with as little as 2.85 m of free space, thanks to its low turning radius. Like all our vehicles, Rocla ART complies with the ISO 3691-4 safety standard and includes numerous safety features and scanners as a default. Additionally, Avant Tecno ARTs are equipped with overhead laser scanners to effectively detect surrounding traffic and obstacles. These safety features have made it possible for a shared environment like this to become safer as efficiency improves.
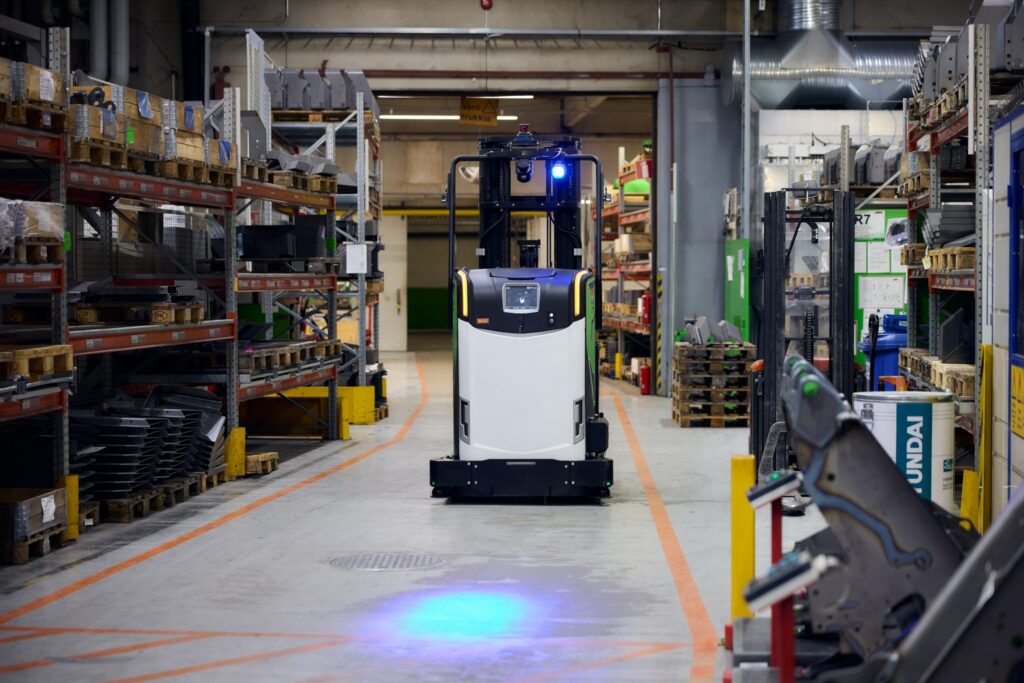
The ARTs Hautamäki, Jönssi, and Dille pick up welded front and rear frames from the welding department and transport them to the painting process. After painting, AGVs deliver the painted components to a high buffer warehouse and, finally, from the buffer warehouse to the roller tracks of the assembly line. “In our assembly line, we have a takt time of 14 minutes, so precision in every logistics operation is crucial. Rocla AGVs have enabled us to have the right number of components at the right time,” explains Pesola.
When the assembly line consumes a front frame of a certain type, the MES system sends an immediate kanban task based on real-time consumption to the welding department to weld a new frame and creates a request on FleetController for an AGV to bring a new frame from the buffer to the assembly line.
After the new frame has been welded, an operator inspects the piece and calls for an AGV to pick it up using push buttons that work on I/O logic. This means a different push button exists for each frame size. That way, FleetController knows the location where the ART should deliver the pallet at the paint shop.
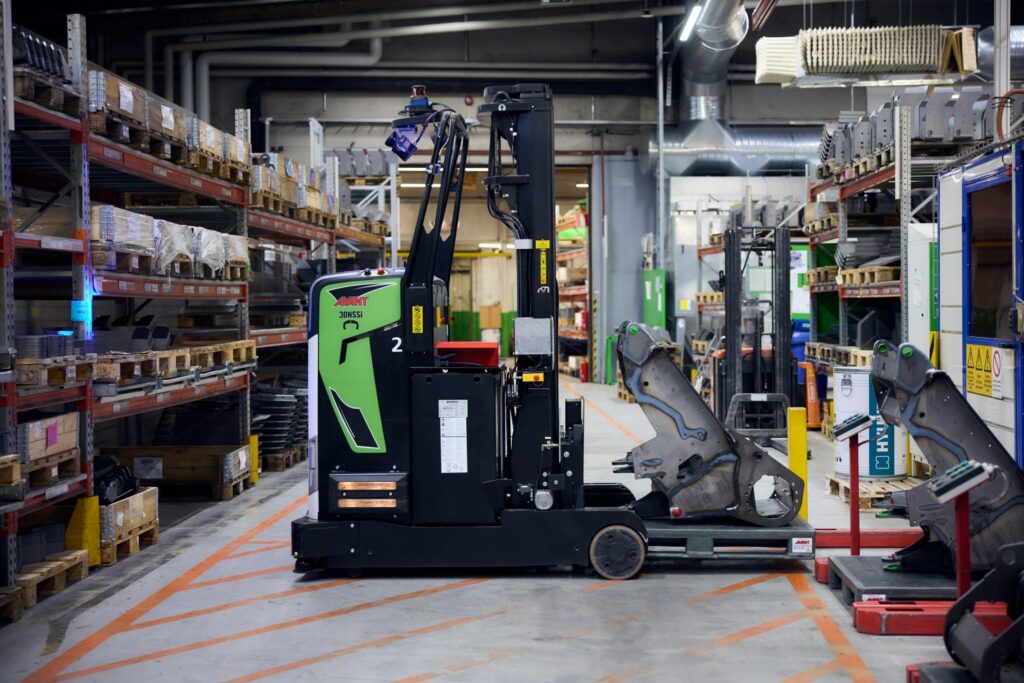
After painting, the frames’ transportation to the supermarket buffer warehouse is activated in the MES/WMS with a tablet. The operator places the frame in a pick-up station, and the FleetController receives the pick-up task through the WMS system. From the buffer warehouse, the painted frames are picked for the assembly line according to kanban calls based on real-time consumption.
Thanks to the seamless integration between Rocla FleetController and the existing MES systems, continuous productivity is ensured without delays, and lead time between different manufacturing processes is minimised. Additionally, The FleetController Dashboard displayed on a screen at the heart of the factory, is actively monitored by operators for quick response to any incidents that might disrupt the flow of operations.
“FleetController has been an essential part of the entire AGV process. It has provided us with the visibility to fine-tune task priorities between different departments and the information needed to troubleshoot problems of any kind,” adds Pesola.
Avant Tecno improved the internal material flow thanks to Rocla AGVs
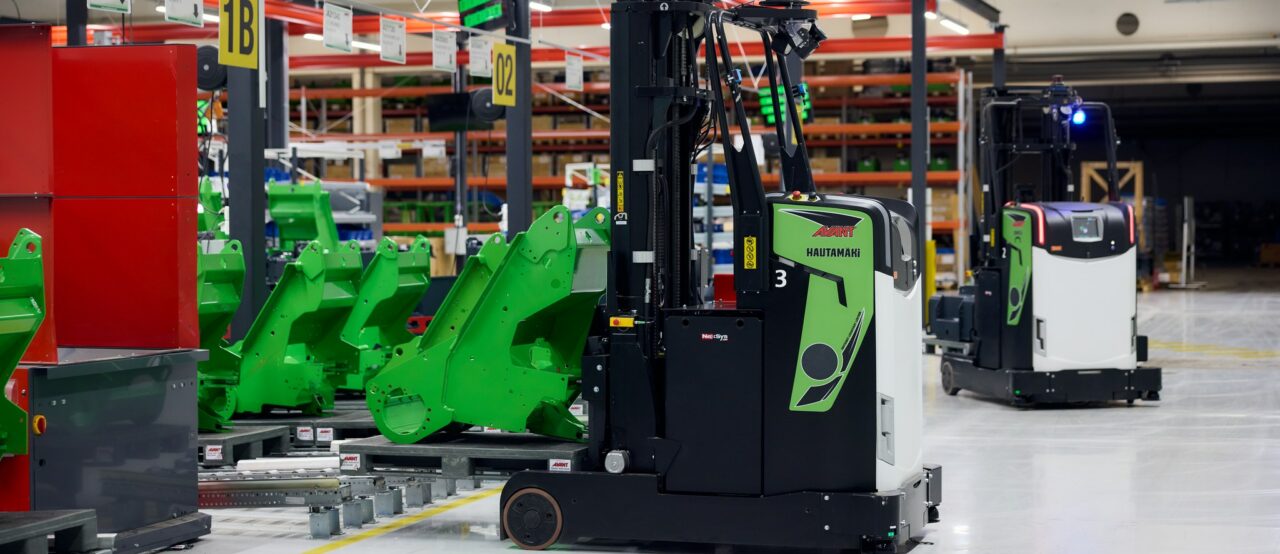
Maximising the solution’s lifespan with Logisnext’s Full service agreement
Even when an AGV solution complies with relevant safety standards, such as ISO 3691-4, preventive maintenance remains crucial. This proactive approach helps intercept potential future failures in your AGV system. Regular maintenance audits ensure that the vehicles meet industry standards and regulations, addressing potential issues before they escalate into major problems.
Timely reactions to potential threats can prevent expensive repairs and replacements. Therefore, selecting the right service package is essential for ensuring the longevity of your AGV fleet. This choice ensures that the solution continues to contribute to smoother operations and high productivity, with AGVs operating safely, reliably, and efficiently.
During the project implementation, Avant Tecno learned about our comprehensive service packages and selected the Full service agreement as it best suited their needs. “We were new to AGV technology and wanted to have them monitored and serviced by an expert team if needed. For peace of mind, we chose the Full service package so that we could focus more on the operational side of things,” says Pesola.
The Full service package includes:
- A maintenance audit
- Preventive maintenance
- Software maintenance
- Email support
- 24/7 AGV Helpdesk support
- Spare parts and work on unexpected failure
“I would recommend the Full service agreement to all customers who are new to this technology or don’t necessarily have a large maintenance department,” concludes Pesola.
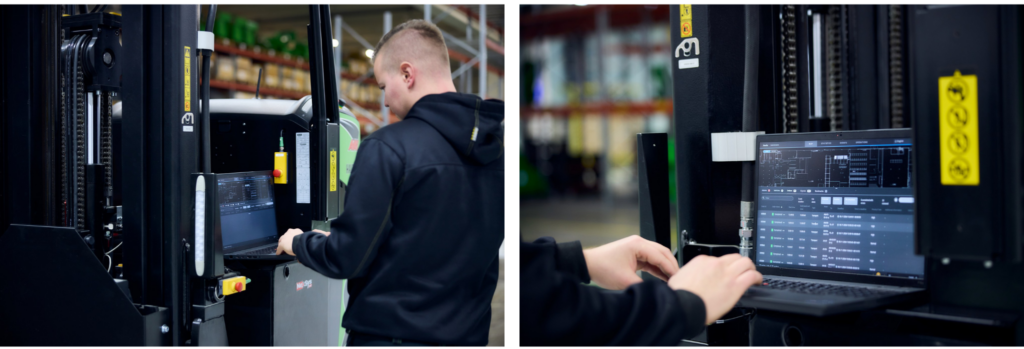
Results
The Rocla AGV Solutions team implemented a solution that would improve the transport of heavy welded components between the two buildings, overcoming challenges such as a steep ramp connecting them where traffic is high, and visibility is minimal, achieving the ultimate goal of transitioning from a push to a pull process. Pesola explained that this change “dramatically reduced the number of missing components and gave a much better understanding about the bottlenecks in our processes,” thereby improving transparency and traceability in Avant Tecno’s operations.
Additionally, thanks to the implementation of the AGV solution with a comprehensive service package, overall warehouse safety has been significantly strengthened. The safety of frame transports has improved because AGVs eliminate the need to transport excessive loads at once. This change has also enforced good practices in the packaging of parts and the use of pallets, ensuring the safety of other workers in the area.
Avant Tecno continues to grow, with a keen focus on the future. The company is exploring the potential of integrating more AGVs and new technologies to stay ahead of the curve and efficiently meet the demands of a fluctuating market.